Phygital Discovery: Key to Agile Development of Physical Products

Differences between software and hardware prototypes
Just to get this straight up front: There is little difference in the understanding of the concept of discovery between software and hardware. Of course, there are a lot of different interpretations out there, but the hardware does not necessarily add new ones.
The basic understanding that product discovery is about continuous and fast learning of what to build is the same. And the dimensions to consider are the same, too: Customer value, usability, feasibility, and stakeholder support (as stated by Cagan, 2017) are true for software and hardware the like. Sustainability needs to be added, but that is a topic of its own and, again, just as important for software as it is for hardware.
Also, the object of product discovery is the same: In the end, it’s about prototypes/MVPs, i.e., preliminary products that are just good enough to be tested as early and quickly as possible in order to avoid building something that offers no value, is hard to use, cannot be produced, lacks stakeholder support and is an environmental mess.
So far, so good, but with prototypes, the software and hardware paths diverge, and the protagonists follow them at different speeds and use different techniques. To take it to the extreme: In Software, it is fairly easy to build prototypes, and there are tools like Figma or Axture that help to create ones that look quite close to finished solutions – or are even finished solutions if Low- and No-Code tools can be applied (Johannessen & Davenport, 2021).
Also, everything takes place in basically one discipline: Coding. When it comes to iterations, there are all the modern agile and lean tools that help to organize the activities.
In Hardware, things are a bit, well, harder. Apart from the very first ideas, where maybe a simple paper sample can be used to demo a product, meaningful iterations soon require prototypes made of the intended material. And most of the time, several components made of different materials are needed, of which some need to be bought in.
Despite all advancements in production techniques, including “3D Printing” (generative building techniques, to be more precise), making something real still takes time. And testing it, whether it is a customer or user or feasibility test, often takes even longer. Furthermore, prototypes can often not be easily duplicated and sent for user testing around the world to consider international markets.
Also, feasibility and/or functional tests often run for weeks if the durability of a solution shall be tested. And if something does not work as expected, the production and testing of prototypes need to be repeated so that delays add up and can easily result in not meeting deadlines. In all this, delays caused by logistics or production problems have to be considered too.
Agile management methods help increase flexibility and speed things up
However, it cannot make individual production or testing steps faster. And in reality, even perfectly agile-trained teams tend to fall back into traditional waterfall habits because manufacturing and sourcing the various prototype components requires the coordination of familiar processes for which project plans are perfectly suited. Since part of the work follows a waterfall approach for good reasons, the team can easily remain stuck in or fall back into waterfall thinking.
Even if teams manage to use the appropriate tools in the respective contexts, long manufacturing, and testing durations and the fact that real parts are place-bound remain. One way to overcome this is to remain in the digital space as long as possible and work with digital prototypes. The tools to do that are well known. Parts and components have long been designed in CAD programs, and creating digital prototypes are fast, easy, and established (Grieb, 2010, p. 52). The key to speed is to utilize the full potential of digital prototypes.
When it comes to assessing customer value and usability, virtual (or augmented) reality tools can be utilized for testing. The applications are available and are getting better and better (Pfeiffer, 2021). However, without knowing if an idea is feasible at all, the level of confidence may not be high enough even to start such virtual UX-testing activities. The level can be increased by using simulation tools to virtually test parts and components, which has long become a common design approach (Karlberg et al., 2013, S. 70).
Typically, simulations are based on designed CAD models using FEM and/or CFD methods (Lashin & Stark, 2021, pp. 1144). In that case, simulations do not consider the production characteristics of the simulated parts. Therefore, they cannot reliably predict how the real part will behave, which is one of the reasons why real prototypes are eventually produced and tested.
Transforming experience into data is the big challenge
Transferring the part data from a CAD- into a simulation system is prone to data errors which can result in extensive manual repair work (Lashin & Stark, 2021, S. 1146). This may be a reason why adding simulation steps and making simulations even more complex and lengthy rarely happens.
However, by adding steps, the prediction quality of simulations can be increased substantially, as, e.g., Zimmerling et al. (2019) show. In the first step, the manufacturing of the parts is simulated so that virtual components are obtained that approximate reality to a very high degree. These are then used in functional simulations in subsequent steps.
If the prediction quality can be increased to a level where making and testing real prototypes can be postponed until the very end of the development process, the goal of remain in the digital space as long as possible and work with digital prototypes is achieved.
Such multi-step or -stage simulations are costly and require a lot of computation power, even if artificial intelligence techniques will help to reduce costs in the future (Zimmerling et al., 2019, S. 5).
The main advantage of remaining in the digital space as long as possible is that idea, and design iterations can be performed fast and at a high level of feasibility confidence. And this is what makes it interesting for product discovery.
Similar to software, hardware discovery can emphasize early phases stronger, can perform more iterations, and can obtain user and customer feedback before actually building anything. In other words, this approach is an enabler for true product discovery measured by software terms.
Why is it then that this approach, although well known, is not yet widely used in the hardware world?
In addition to the significant cost and likely shortage of development-oriented simulation experts, the main challenge is obtaining the data needed to perform meaningful first-stage simulations. Otherwise, it’s garbage in, garbage out. This job can be dubbed as transferring experience into data and is a special task of digital transformation.
Companies with a strong legacy in R&D, product development, and production (like many German Mittelstand companies) sit on busloads full of experience and test reports that could be exploited to a higher degree than so far. The more plentiful the information, the better its quality is, and the better it gets fed into simulations, the more trustworthy the results will be. It takes a lot to cope with this challenge. We will explain in further posts what that is and how to tackle the challenge.
Autor
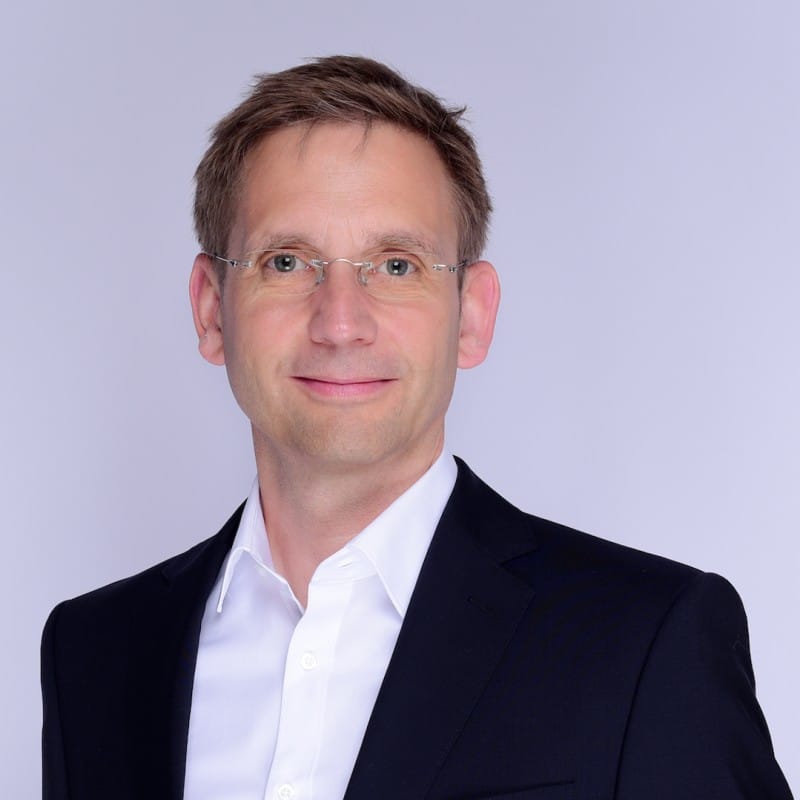
Prof. Dr. Lars Ilius
Head of Phygital at TalentFormation.com GmbH, Hamburg. Lars presented this topic on stage at the conference Solutions 2022 in Hamburg.
If you find this interesting, please also consider reading our article about Phygital Product Development by Daniel Neuberger, Head of Product Coaching at TalentFormation.
TalentFormation is a Company Rebuilder that helps bigger companiestransform their organization and develop, implement and operate new digital business models to perform and grow sustainably.
Together with a growing network of tech service providers, solopreneurs and freelancers, TalentFormation forms highly effective product teams that enable companies to compete with disruptive competitors. For small business owners, we provide the environment to build and scale their company within the TalentFormation Network.
Founded in 2009 in Hamburg, we focus on Company Rebuilding projects in Consumer Products, Mobility, Health, Energy, and other future-proof industries, both for manufacturers and retailers.